lerail.com
24
'21
Written on Modified on
ALSTOM UTILISE L'IMPRESSION 3D FDM DE STRATASYS POUR CRÉER DES PIÈCES DE RECHANGE D'URGENCE ET MINIMISER LES TEMPS D'ARRÊT DU RÉSEAU DE TRAMWAY DE SÉTIF
Alstom, leader mondial de la mobilité verte et intelligente, a réduit ses délais de production de pièces de rechange de 45 jours à 48 heures, grâce aux imprimantes 3D F370. L’entreprise a également permis au réseau de tramways de Sétif d’économiser environ 6 000 euros grâce à l’impression à la demande de ses pièces de rechange en 3D, par rapport aux méthodes de production traditionnelles.
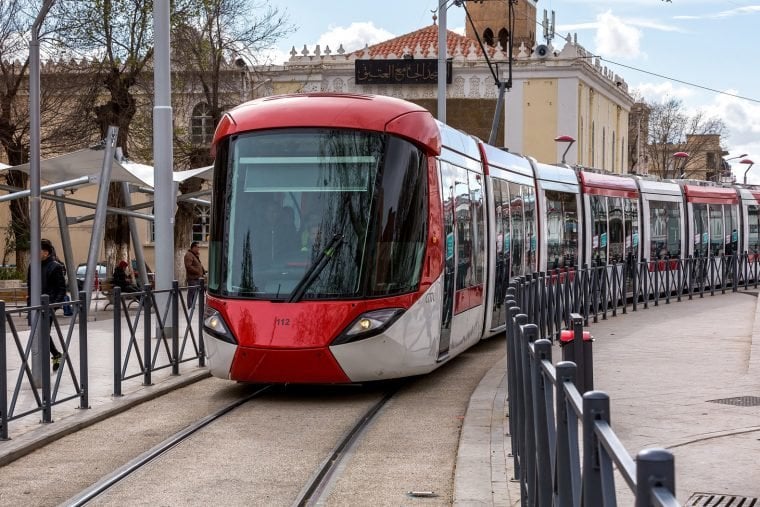
Alstom aide les entreprises à s’orienter vers la faible émission de carbone, et développe et commercialise des solutions de mobilité qui constituent les bases durables de l’avenir des transports. L’entreprise innove dans la production de pièces de rechange en faisant appel à l’impression 3D par fabrication additive pour ses opérations de maintenance et de réparation à la demande. En mettant à profit cette technologie, Alstom réduit au maximum le délai d’attente de ses clients et permet aux réseaux de transport de rester opérationnels.
« La flexibilité offerte par l’impression 3D est pour Alstom un atout stratégique incontournable », explique Aurélien Fussel, responsable du programme de fabrication additive chez Alstom. « Lorsque la continuité des opérations de nos clients dépend des pièces de rechange, cette capacité de production interne nous permet de contourner notre chaîne d’approvisionnement traditionnelle et de leur proposer rapidement une solution rentable qui répond à leurs besoins. »
Pièces de rechange urgentes imprimées en 3D et livrées sous 48 heures
Grâce à une telle souplesse de fabrication, Alstom a récemment pu éviter à l’un de ses clients, le réseau de tramways algérien de Sétif, d’attendre environ 45 jours et de dépenser inutilement plusieurs milliers d’euros suite à un problème de maintenance. Sétif a découvert que les phares de tramway se cassaient sous l’effet de l’accumulation d’eau et de pierres qui s’introduisaient à travers de petits orifices. L’entreprise s’est donc tournée vers Alstom pour lui demander de toute urgence des pièces de rechange permettant de boucher ces orifices et d’éviter d’endommager davantage les tramways.
Grâce à son hub interne dédié à l’impression 3D, Alstom a mis en œuvre son imprimante 3D Stratasys F370 basée sur la technologie FDM® pour fabriquer un drainage en caoutchouc et boucher les orifices sur les phares de ses tramways. L’entreprise a pu en concevoir, fabriquer et livrer une douzaine, en seulement 48 heures.
« Nous avons évité le délai de production minimum de trois semaines généralement requis avec les méthodes de fabrication traditionnelles et nous avons pu éviter l’interruption du réseau de tramway », explique A. Fussel. « Pour nos clients du secteur des transports comme Sétif, chaque minute d’arrêt d’exploitation sur un réseau entraîne une perte de revenus ; et chaque minute de gagnée dans la résolution d’un problème de maintenance permet ainsi de minimiser cette perte. »
Mis à part la limitation des temps d’arrêt, l’utilisation de l’impression 3D FDM de Stratasys pour remplacer des méthodes de moulage ou de coulée plus coûteuses et nécessitant beaucoup de main-d’œuvre a permis à Sétif de faire des économies supplémentaires, se chiffrant par une réduction de 80 % des frais fixes. Dans l’ensemble, le projet a permis à Sétif d’économiser environ 6 000 euros de frais fixes.
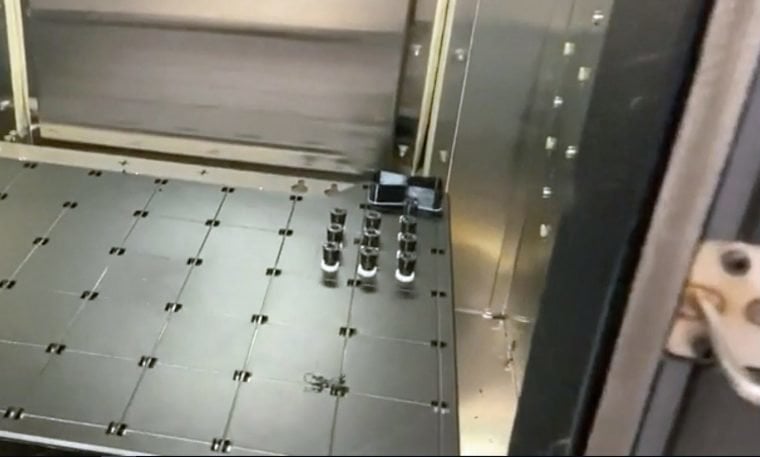
Les matériaux de production avancés ont prouvé leur nécessité
Pour Alstom, produire des pièces de rechange uniques, réduire des coûts élevés et éviter les longs délais exigés par l’outillage conventionnel représentent de précieux atouts. Toutefois, comme l’explique Jaume Altesa, responsable du hub d’impression 3D d’Alstom à Barcelone, ce projet n’aurait pas été possible sans des matériaux d’impression 3D avancés, robustes, capables de supporter les conditions difficiles imposées par des véhicules de transport lourds en mouvement.
« Disposer de matériaux de production est essentiel pour fournir à nos clients des pièces imprimées en 3D prêtes à être installées sur des véhicules », poursuit J. Altesa.
Les bouchons de drainage en caoutchouc pour Sétif, par exemple, ont été imprimés en 3D par Alstom dans un matériau élastomère avancé hautement durable : le FDM TPU 92A. Associant d’excellentes performances en matière de flexibilité, d’étirement et de résistance à l’abrasion et à la déchirure, ce matériau élastomère s’est avéré idéal pour répondre aux exigences d’une utilisation extérieure soutenue. Ces pièces sont encore en fonctionnement aujourd’hui.
« Comme nous l’avons vu pendant la COVID-19, à certains égards, l’impression 3D a connu un tournant, avec de plus en plus de fabricants adoptant la technologie pour augmenter leur flexibilité de production et réduire leur dépendance de la chaîne d’approvisionnement », commente Yann Rageul, responsable de l’unité de fabrication pour la zone EMEA, Stratasys. « En tant que client de longue date, Alstom est un brillant exemple de ces entreprises pionnières qui, depuis de nombreuses années, utilisent la fabrication additive pour produire des pièces de rechange. Il ne s’agit pas seulement pour l’entreprise d’optimiser ses propres performances, mais aussi de fournir à ses clients des solutions innovantes qui seraient tout simplement impensables par fabrication traditionnelle. »
Alstom a participé au projet de Sétif en Algérie en 2018 par la fourniture de quelque 26 unités Citadis pour le premier tramway public de la ville. L’entreprise, qui déploie ses activités dans le pays depuis plus de 60 ans, a également fourni des systèmes de tramway intégrés aux villes d’Alger, d’Oran et de Constantine.
www.stratasys.com