Le rôle croissant de la fabrication additive dans le secteur ferroviaire : Les spécialistes en parlent
Dans le monde, les entreprises ferroviaires doivent faire face à des difficultés croissantes pour construire les trains et en assurer la maintenance de plus en plus rapidement, et à moindre coût.
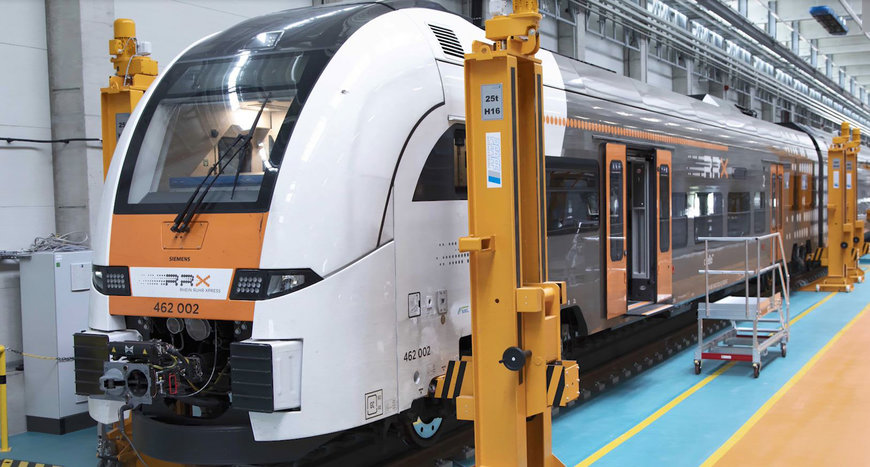
Dans leur recherche d'excellence en matière technique et de conception, les réglementations les plus strictes concernant les matériaux et les fonctionnalités applicables au secteur ferroviaire ajoutent une complexité supplémentaire à la production de nouvelles pièces, ou de pièces détachées. Pour répondre aux exigences du secteur, les principales entreprises de transport européennes, Bombardier Transportation, Deutsche Bahn ESG et Siemens Mobility se sont toutes tournées vers la technologie de fabrication additive. Dans cet entretien, des spécialistes de ces entreprises nous font part des contraintes inhérentes à la production dans le secteur ferroviaire, et nous expliquent comment ils parviennent à les alléger avec l'aide de la fabrication additive.
- AB : André Bialoscek, responsable de l'intégration physique des véhicules chez Bombardier Transportation, Hennigsdorf
- MS : Martin Stevens, responsable de l'ingénierie mécanique chez Deutsche Bahn ESG
- MK : Michael Kuczmik, responsable de la fabrication additive et des services de mobilité pour les clients chez Siemens Mobility
1. Pourriez-vous nous préciser la structure du secteur ferroviaire au Royaume-Uni et en Allemagne, en ce qui concerne les relations entre les exploitants, les sociétés de maintenance et les fournisseurs de matériel roulant, ainsi que le rôle joué par chacun d'entre eux ?
MK : Dans toute l'Allemagne, les exploitants ferroviaires se chargent du fonctionnement quotidien des trains et jouent le rôle de régisseurs du transport public. Les sociétés de maintenance sont quant à elles responsables de garantir la disponibilité, et parfois d'améliorer l'attrait des trains, tandis que les fabricants de matériel roulant peuvent être définis comme ceux qui se chargent de fournir les véhicules et infrastructures ferroviaires aux propriétaires, qu'il s'agisse d'exploitants ou de sociétés de location. En ce qui concerne Siemens, nous sommes capables d'assumer chacun de ces rôles, ce qui fait que nous sommes en mesure d'offrir à nos clients un portefeuille complet de services, en fonction des circonstances et de la demande.
AB : Notre fonctionnement est similaire chez Bombardier. Nous sommes parfois le seul fournisseur de matériel roulant, mais nous sommes aussi responsables de la maintenance et du fonctionnement effectif des réseaux ferroviaires. Tout dépend du modèle commercial de nos clients.
MS : Au Royaume-Uni, tout cela est assez fragmenté. Les fournisseurs de matériel roulant financent les trains et les louent aux exploitants ferroviaires. Les exploitants assurent quant à eux les services ferroviaires quotidiens et se chargent des tâches de maintenance de base. Mais nous avons aussi des sociétés de maintenance et de réparation qui réalisent la remise à neuf et les révisions de grande envergure, ainsi que des sociétés d'assistance technique comme DB ESG, qui fournissent des services techniques au secteur.
2. Traditionnellement, quels sont les principaux défis généralement liés à la production ferroviaire ?
MS : À tous les niveaux, le plus grand défi concerne les très faibles volumes de production. Une grosse commande de 800 M£ pour la fabrication d'un nouveau train se traduit par la production d'un maximum de 100 rames. Il s'agit là d'un volume bien trop faible pour une production en série typique. Ajoutons à cela que les trains peuvent fonctionner pendant 40 ans, ce qui donne lieu aujourd'hui à un très grand nombre de conceptions différentes en service, chacune d'elles n'étant représentée que par peu de trains. L'approvisionnement des pièces de rechange constitue donc un véritable défi, dans la mesure où vous ne pouvez pas recourir aux techniques de production en série pour les fabriquer.
MK : Je me rallie au sentiment que les faibles volumes de production représentent un véritable défi. Certains trains ont parfois une durée de vie de 60 ans. Des coûts ponctuels élevés, et parfois des délais trop importants, peuvent entraîner, dans le pire des cas, leur obsolescence. Il existe surtout un défi de toute première importance, qui réside dans la compréhension et le respect des réglementations applicables à des cas d'utilisation spécifiques : c'est là un prérequis absolu. En ce sens, vous ne pouvez faire appel qu'à des fournisseurs qualifiés.
AB : Aujourd'hui, il nous faut livrer des trains beaucoup plus rapidement qu'il y a trois ou cinq ans. La pression est donc très grande sur toutes les facettes de nos activités, de l'ingénierie à l'approvisionnement, en passant par la fabrication, les tests et l'homologation. Nous devons constamment et rapidement nous adapter au marché, qui est en évolution permanente, et cela est souvent une véritable gageure pour une entreprise cherchant à conserver sa longueur d'avance. Et c'est précisément là que la fabrication additive a son rôle à jouer.
3. Très intéressant. Dans quelle mesure la fabrication additive est-elle donc capable de contribuer à la résolution de tels défis de production ?
AB : La fabrication additive est la bonne approche, et une avancée significative dans le monde des sociétés de transport. Grâce à elle, nous pouvons rapidement créer des pièces physiques ayant des dimensions réalistes tout au long du processus de validation de la conception de nouveaux trains, et pas seulement des prototypes, car cette technologie s'applique également à la production de pièces en série. Un aspect tout aussi important est le service à la demande, pour lequel la fabrication additive apporte des avantages considérables : remplacer des pièces obsolètes, produire de petits volumes, ou encore revoir la conception de certaines pièces.
MK : Siemens Mobility a adopté cette technologie depuis longtemps, et même créé un service spécialement dédié à la fabrication additive. Il s'agit d'une équipe de 18 personnes qui aide nos clients internes et externes à résoudre leurs problèmes techniques et à réaliser des pièces détachées par fabrication additive. Nos clients peuvent commander des pièces à la demande à travers notre Easy Spares Marketplace, si leurs délais de livraison le requièrent. En cas de besoin, nous pouvons même revoir des conceptions de 30 ans d'âge, parfois en collaboration avec les clients.
MS : La fabrication additive représente également une part considérable de notre activité. Elle est parfaitement adaptée aux passes de fabrication en faibles volumes, dans la mesure où elle permet de transformer simplement une conception en impression tout en éliminant les coûts de l'outillage et les contraintes en matière de délais. Par exemple, seule la fabrication additive est capable de réaliser cinq ouvertures d'aération pour une flotte réduite de trains. Même si le coût de chaque unité individuelle est élevé, vous avez la possibilité de n'en fabriquer que cinq et de les recevoir en une quinzaine de jours, au lieu d'avoir à en acheter 10 000 et de vous les faire livrer dans trois mois.
Les avantages, qui sont gigantesques, compensent largement les quelques inconvénients. De fait, nous avons récemment travaillé en collaboration avec Angel Trains, l'un des plus gros fournisseurs de matériel roulant au Royaume-Uni, et avec l'exploitant ferroviaire Chiltern Railways, pour déployer et tester avec satisfaction les premières pièces imprimées en 3D destinées à des trains de voyageurs britanniques.
4. Martin, vous avez mentionné les ouvertures d'aération comme exemple de ce que vous pouvez produire par la technologie de la fabrication additive. Chacun de vous pourrait-il nous donner ses propres exemples ?
MS : Nous fabriquons plusieurs types de pièces pour les trains de Chiltern Railways, notamment des poignées d'intérieur. Les pièces originales étaient en aluminium moulé, et leur conception est aujourd'hui obsolète. Ces pièces n'ont que rarement besoin d'être remplacées, mais l'exploitant était en rupture de stock, et le cas échéant, il est impératif de les réparer en l'espace d'une semaine pour pouvoir respecter les réglementations. La fabrication additive est parfaitement adaptée à ce genre de situation, car elle nous permet de produire rapidement cinq exemplaires dans un matériau comme la résine ULTEM 9085, qui respecte les exigences en matière de comportement au feu, fumée et toxicité.
MK : Dans notre cas, nous produisons des parties de carénage frontal pour des véhicules légers sur rail (ou tramways). Il s'agit ici d'un exemple d'utilisation après-vente. Les tramways partagent les voies avec d'autres véhicules ferroviaires, ce qui est à l'origine d'un grand nombre d'accidents. Nos pièces imprimées sont capables de remplacer des sections endommagées comme les jupes avant, et peuvent être livrées en quelques jours au lieu de plusieurs mois. Nos clients peuvent commander une pièce au lieu de 10, et n'ont pas besoin de remplacer la totalité de la jupe avant, sinon seulement une partie. Cela signifie par ailleurs que le travail peut être effectué par une seule personne, plus rapidement et à moindre coût.
AB : Pour en revenir aux ouvertures d'aération, nous avons été capables de réduire le temps de production d'une pièce du système de distribution d'air de quatre mois à environ quatre semaines, grâce à la technologie de fabrication additive de Stratasys. Le résultat a été un gain de temps d'environ 77 %, ce qui est un avantage considérable pour notre département. Il s'agit là d'un parfait exemple de notre capacité à fabriquer certaines pièces à la demande sur la base de nos propres exigences, sans dépendre de longs délais de production ni faire de compromis quant à la qualité des matériaux.
5. Tout cela paraît merveilleux, mais qu'en est-il de la certification des pièces imprimées en 3D ?
AB : En ce qui concerne le système de distribution d'air, la plus grande partie a été imprimée en 3D avec de la résine ULTEM 9085 sur notre F900 de Stratasys, ce qui a permis de réduire considérablement le poids du composant et d'optimiser la quantité totale de matériau utilisée. Et ce qui est important, c'est que la résine ULTEM 9085 est conforme aux exigences de certification de la norme EN 45545-2 en matière de comportement au feu, fumée et toxicité dans le secteur ferroviaire, que doivent vérifier tous les composants de trains produits chez Bombardier Transportation.
MK : En général, les certificats font référence aux propriétés des matériaux, comme le comportement au feu et l'allongement à la rupture, ainsi qu'aux calculs spécifiques concernant la résistance de certaines pièces. Dans la mesure où les pièces peuvent avoir un impact important sur la sécurité, une mise à jour de l'analyse des risques sur l'ensemble du système est souvent nécessaire. Pour cette raison, nous utilisons également le matériau ULTEM 9085, qui respecte les normes de sécurité en matière de comportement au feu.
MS : Je pense que nous sommes tous d'accord sur le fait que chaque pièce installée à bord d'un train a besoin d'une évaluation de conformité. Il est nécessaire de démontrer que les pièces respectent les exigences les plus strictes du secteur ferroviaire en matière de comportement au feu, et qu'elles sont suffisamment résistantes pour supporter un cas de charge prédéterminé.
6. En ce qui concerne la production de pièces détachées pour le secteur ferroviaire, que pensez-vous du stockage numérique ?
MS : Des millions de livres sterling sont mobilisées pour constituer des stocks de pièces de rechange destinées aux parcs ferroviaires britanniques. Or, une bonne part de ces pièces pourraient bien ne jamais être utilisées. L'adoption du stockage numérique pour les pièces les plus simples est sans aucun doute la direction à suivre.
MK : J'irais même un peu plus loin. Nous sommes convaincus que le passage au stockage virtuel est essentiel pour aller de l'avant. Tout au moins pour les pièces détachées utilisées dans la maintenance corrective, dans la mesure où nous ne savons pas exactement si elles seront vraiment nécessaires, ni à quel moment, ni selon quelle fréquence. Chez Siemens Mobility, nous offrons déjà cette possibilité à travers notre concept Easy Sparovation. Nous proposons plusieurs options : commande standard selon les délais de livraison habituels imposés par les contraintes de la production conventionnelle ; livraison en vingt-quatre heures en Europe à partir de nos propres stocks ; ou impression à la demande. La société de maintenance ou l'exploitant prend sa décision en fonction de l'urgence de ses besoins.
AB : Bien sûr, il s'agit là pour nous aussi d'un aspect essentiel. Au fur et à mesure que la fabrication additive occupera une place plus importante dans la production en série et permettra de remplacer de plus en plus de pièces ferroviaires réalisées par des méthodes traditionnelles, nous pourrons vraiment tirer parti du plein potentiel du stockage numérique.
7. Il ne fait aucun doute que la fabrication additive a jusqu'ici joué un rôle important pour vos entreprises, mais vers quelles autres futures applications vous orientez-vous ?
AB : Nous attendons de voir les nouveaux développements dans le domaine de la technologie de fabrication additive et des matériaux disponibles sur le marché. C'est un aspect important à prendre en compte pour pouvoir relever les futurs défis de la production dans le secteur ferroviaire. La capacité à imprimer des pièces d'encore plus grandes dimensions serait une avancée extraordinaire, et je suis sûr que nous serons tous d'accord sur ce point.
MK : Absolument, ce serait fantastique de pouvoir imprimer des pièces plus grandes. Pour l'instant, nous avons l'intention d'augmenter nos cas d'utilisation de pièces détachées en collaboration avec nos clients internes et externes, ainsi que dans le cadre des nouvelles conceptions de véhicules. Nous allons également procéder à la mise en œuvre de notre réseau mondial d'imprimantes, et à l'interconnexion de ce réseau avec notre MES (système d'exécution de fabrication) commun. Cela nous permettra d'améliorer les délais et de réduire les coûts, grâce à une production plus localisée.
MS : Pour ce qui est de l'avenir, notre prochaine étape consistera à élargir ce que nous avons fait pour Chiltern Railways aux 27 autres exploitants ferroviaires du Royaume-Uni. En collaboration avec Angel Trains, notre objectif pour 2020 est d'utiliser la rétro-ingénierie pour fournir deux ou trois pièces aujourd'hui obsolètes à chaque exploitant. Ce sera la manière la plus efficace de faire connaître au secteur ferroviaire le potentiel de la fabrication additive.
Encadré : Le point de vue du fabricant d'impression 3D : quelques mots de Yann Rageul, directeur des solutions de fabrication chez Stratasys
Les avantages de la fabrication additive en matière de faibles volumes répondent aux exigences de production du domaine ferroviaire. Il n'est donc pas étonnant que la technologie fasse aujourd'hui partie intégrante des processus opérationnels des principaux fournisseurs du secteur. Au cours trente dernières années, la fabrication additive a mûri, et l'éventail des applications possibles s'est considérablement élargi. L'impression 3D est désormais un outil de qualité industrielle que les fournisseurs ferroviaires peuvent utiliser pour sécuriser leurs approvisionnements en pièces détachées, créer des outils capables de simplifier leurs tâches de maintenance ou leurs opérations, ou encore améliorer la sécurité et l'expérience de leurs clients.
Tandis que de plus en plus de compagnies ferroviaires optimisent l'emploi de la fabrication additive par la constitution de stocks numériques, la production de pièces détachées à la demande, là où elles sont nécessaires et dans la quantité exacte requise, peut devenir une réalité. Il devient ainsi possible non seulement de réduire le besoin de stockage et d'entreposage de pièces, mais encore d'écourter de façon significative les délais nécessaires à la maintenance et la réparation des trains. Pour toutes les entreprises disposées à adopter ce nouveau modèle commercial, l'avenir n'est jamais trop éloigné.
www.stratasys.com